Identify the Right Sensor for Level Monitoring Needs
Key Factors in Selecting Level Monitoring Sensors
Material Type: Liquid vs Solid Detection Requirements
Understanding the specific needs for detecting different materials is crucial. Liquid sensors often require specialized sealing and pressure ratings to function properly under varying conditions. Meanwhile, solid sensors need to account for the varying bulk densities to ensure accurate measurements. It's also essential to factor in a sensor's sensitivity and range; for instance, liquid sensors might not properly detect solids and may require operational adjustments.
Environmental Conditions and Sensor Durability
Evaluating the installation environment is vital, as temperature fluctuations, humidity levels, and exposure to chemicals can greatly impact a sensor's functionality and lifespan. Ensuring sensors are equipped with suitable durability requirements, like IP ratings for ingress protection, is crucial. For example, an IP67-rated sensor can withstand dust and immersion in water, making it ideal for use in harsh conditions.
Accuracy Needs for Industrial Applications
For industrial applications, high precision is often required to meet the stringent demands of quality control and efficiency. Understanding the necessary tolerance levels for specific processes can be crucial. Industry reports often highlight the benefits of high-accuracy sensors in reducing waste and improving production efficiency, demonstrating their economic value in industrial settings.
Integration With Existing Control Systems
Ensuring sensors can easily integrate with existing control systems is paramount to seamless operations. This involves understanding communication protocols, such as Modbus or RS-485, that allow for compatibility with existing technologies. Such integration minimizes downtime and installation costs, thereby enhancing the overall return on investment.
Capacitive Proximity Sensors for Dual-Purpose Monitoring
AC M18-M12 Brass Capacitive Type Features
The AC M18-M12 brass capacitive sensor is engineered for high durability and versatility, making it effective for both liquid and solid detection across diverse industrial applications. Its robust construction ensures that it can endure challenging environments, which is crucial for industries where consistent monitoring is required. This sensor's dual-purpose capabilities make it an ideal choice for environments that necessitate precise detection and the ability to handle a variety of materials.
AC M30 Plastic Cable-Type Sensor Benefits
The AC M30 plastic type sensor offers significant advantages due to its lightweight construction, making it ideal for dynamic installations where ease of deployment is a priority. Its design enhances versatility and cost-effectiveness, allowing it to address various monitoring needs effectively. Industries ranging from large-scale to smaller operations can benefit from its adaptable features, ensuring that costs are kept manageable without sacrificing performance or reliability.
AC M30-M12 Compact Capacitive Solution
The AC M30-M12 sensor serves as a compact solution, providing reliable performance in environments where space constraints limit the use of larger sensors. This compact design focuses on efficiency, leveraging advanced technology to enhance detection accuracy for a variety of materials, including challenging conditions where close monitoring is paramount. Its efficacy in small spaces makes it a valuable tool in applications demanding strict and precise monitoring capabilities.
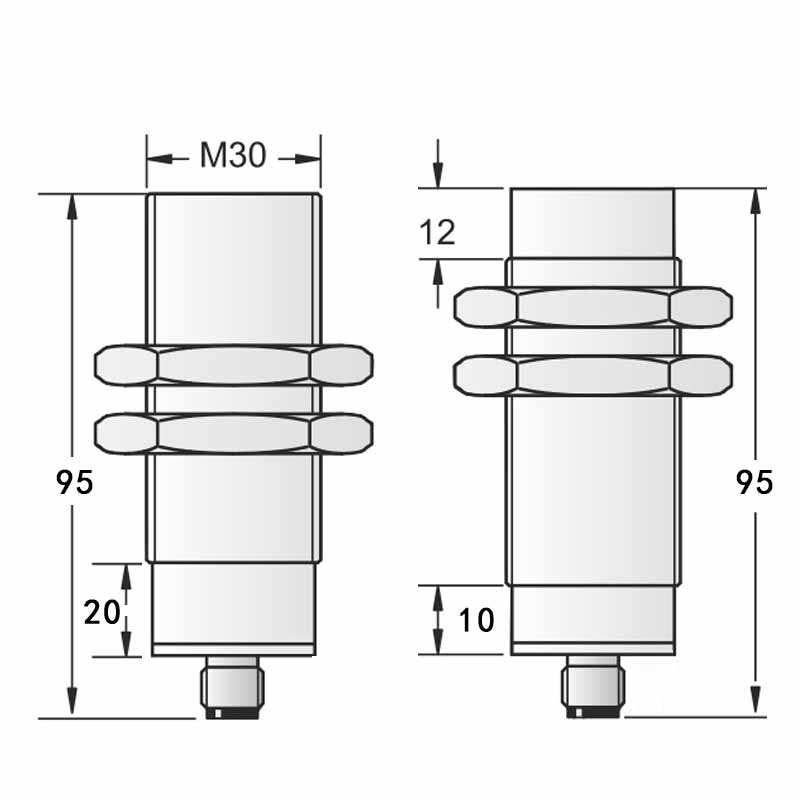
Comparing Sensor Technologies for Liquids vs Solids
Capacitive vs Inductive Proximity Sensors
Capacitive sensors excel in detecting both liquids and solids due to their design, which allows them to sense changes in material capacitance. This makes them exceptionally versatile across various industries. On the other hand, inductive proximity sensors are more suited for detecting metallic solids, as they rely on electromagnetic fields to detect ferrous materials. To illustrate the differences in performance, industry research consistently shows that capacitive sensors offer superior detection capabilities for diverse materials, including non-metallic substances. This data is crucial for companies looking to choose the appropriate technology based on the material composition of their monitoring environments.
Laser Sensors for Precision Solid Level Measurement
Laser sensors are renowned for their precision in measuring solid levels, which is crucial in applications where accuracy is critical. They are particularly valued in industries like manufacturing, where small discrepancies in measurements can lead to significant issues. Reports indicate that laser sensors reduce measurement errors significantly when compared to traditional measurement methods. This reduction in error enhances process reliability and efficiency, making laser sensors an invaluable tool in production and quality control processes. Their ability to provide consistent, accurate results underscores their importance in various manufacturing applications.
Ultrasonic Solutions for Non-Contact Liquid Monitoring
Ultrasonic sensors offer an effective solution for non-contact liquid level monitoring. These sensors eliminate the risks associated with direct contact, such as contamination or sensor wear over time. By using sound waves to detect the presence and distance of liquids, ultrasonic sensors provide reliable readings without the need for manual intervention. Case studies have shown that implementing ultrasonic solutions can lead to substantial cost savings. The reduction in maintenance requirements and improved accuracy can be particularly advantageous in dynamic environments where liquid levels fluctuate frequently, making these sensors an excellent choice for non-invasive liquid monitoring applications.
Implementation Best Practices
Proper Mounting Techniques for Different Materials
Adopting proper mounting techniques is essential to ensure sensor accuracy and reliability across diverse materials. Various methods, like using brackets for solids, cater to the specific challenges associated with the material being monitored. The literature on sensor installations serves as a valuable resource, offering insights into best practices that enhance performance, particularly in complex environments. These resources help in understanding the nuances of mounting techniques that can mitigate erroneous readings and improve overall sensor functionality.
Calibration Methods for Mixed-Phase Environments
Calibration in environments containing both liquids and solids is crucial for maintaining sensor accuracy. Methods must consider the different properties of these phases to ensure precision. Sensor manufacturers provide guidelines for periodic calibration checks, aiding compliance and ensuring consistent functionality. Regular calibration not only ensures optimal performance but also adapts to the dynamic influences of mixed-phase environments, promoting accurate readings over time.
Maintenance Strategies for Long-Term Reliability
Implementing effective maintenance strategies is key to prolonging sensor functionality and ensuring reliability. Essential practices include regular inspections and preventive maintenance schedules, helping avert potential sensor failures. Industry evidence supports these strategies, underscoring their importance in maintaining sensor efficiency. Establishing these routines can significantly reduce downtime and extend the life of sensor systems, fostering a reliable operational environment.