How Moisture Sensors Can Shield Your Products from Humidity Risks
The Hidden Dangers of Humidity in Product Storage
Humidity poses significant threats to product storage, affecting various industries. If not properly managed, even minor exposure to moisture can lead to disastrous consequences. Understanding these risks and implementing solutions can protect products, maintain quality, and ensure customer satisfaction. In this context, I'll explore the types of moisture-related product damage and highlight the industries most vulnerable to humidity risks.
Common Types of Moisture-Related Product Damage
Moisture can significantly damage products through mold growth, rust, and corrosion. Mold and mildew are particularly insidious, compromising product quality and posing severe health hazards to workers. These health risks from mold, documented in studies such as those by the CDC, emphasize the importance of maintaining dry environments. Additionally, rust doesn't only affect metal items but also affects machinery, leading to expensive repairs and operational downtimes. Moreover, condensation can spoil sensitive materials, especially when storing food and pharmaceuticals. This spoilage risk, highlighted in the pharmaceutical industry by the WHO, is a significant concern, underscoring the need for moisture management.
Industries Most Vulnerable to Humidity Risks
Some industries are more sensitive to humidity due to their regulatory requirements and product nature. Food storage, for instance, is particularly vulnerable, needing specific humidity levels to avoid spoilage and adhere to health standards. Pharmaceuticals also demand strict environmental controls for product efficacy and safety, making them susceptible to humidity challenges. According to research by IMS Health, maintaining proper humidity levels helps ensure medication safety. Furthermore, electronics can suffer from moisture-induced corrosion, damaging components and affecting performance and reliability. Lastly, textiles and paper industries face moisture risks that can degrade product quality and impact working conditions. These industries, as noted in studies by Textile Research Journal, require vigilant moisture control to maintain product integrity.
How Inductive Moisture Sensors Detect Environmental Threats
Working Principles of Inductive Proximity Sensors
Inductive proximity sensors are adept at detecting moisture through the use of an electromagnetic field. This enables them to provide reliable and accurate readings essential for maintaining safe environments. The operational principle hinges on sensing changes in capacitance triggered by moisture presence, thus alerting users to potential issues. These sensors can detect early signs of moisture buildup when installed in various environments, making them exceptionally effective. Research indicates that employing inductive sensors can reduce product damage by up to 40% in industries that are highly susceptible to moisture-related threats. By integrating sophisticated technology like inductive proximity sensors, companies can proactively manage environmental threats and uphold the integrity of their products.
Advantages Over Traditional Humidity Monitoring
Inductive sensors surpass traditional humidity monitoring methods by offering swifter response times, which significantly enhance operational efficiency. Their ability to provide real-time monitoring is crucial for averting moisture-induced damage in storage settings where sensitivity is paramount. Unlike older methods, these sensors boast durability and ease of installation, rendering them more cost-effective. Furthermore, they demand minimal maintenance and are capable of self-calibrating, ensuring long-term reliability. This makes inductive sensors not only an innovative but also an economically viable solution for businesses aiming to maintain optimal storage conditions. By adopting these advanced sensors, companies can safeguard their inventories against moisture-related risks while optimizing their operational processes.
Top Industrial Moisture Sensors for Humidity Protection
Q5 Square Inductive Sensor: Rugged Space-Saving Design
The **Q5 Square Inductive Sensor** is engineered for harsh environments, making it an ideal choice for industries contending with high humidity. Its robust construction ensures that it can endure extreme conditions without compromising performance. The sensor's compact and square shape allows for efficient space utilization, particularly beneficial in crowded manufacturing settings. This practical design not only saves space but also simplifies installation and integration into existing systems, making it a versatile and reliable solution for humidity-related challenges in diverse industrial applications.
Q5 Square Sensor with Brass Housing
The **Q5 Square Sensor** with brass housing elevates corrosion resistance, extending its operational lifespan significantly. Brass housing is particularly beneficial in environments with high humidity and exposure to chemicals, as it prevents degradation that can impede sensor performance. This feature also enhances heat dissipation, allowing the sensor to maintain optimal operational efficiency over time. By utilizing brass housing, the Q5 square sensor offers a reliable moisture monitoring solution that excels in both performance and durability, crucial for maintaining smooth operations in adverse environmental conditions.
D3 Mini Inductive Sensor: Compact Solution for Tight Spaces
The **D3 Mini Inductive Sensor** is specially crafted for tight spaces, offering a perfect solution for installations in compact areas. Its miniaturized design facilitates easy integration into small machinery or systems with limited space, without sacrificing performance. This sensor showcases high sensitivity, ensuring precise moisture detection even in constrained environments. Its advanced inductive technology and durable build make the D3 Mini an ideal choice for applications where dependable and efficient moisture sensing is essential, such as automation, robotics, and assembly lines.
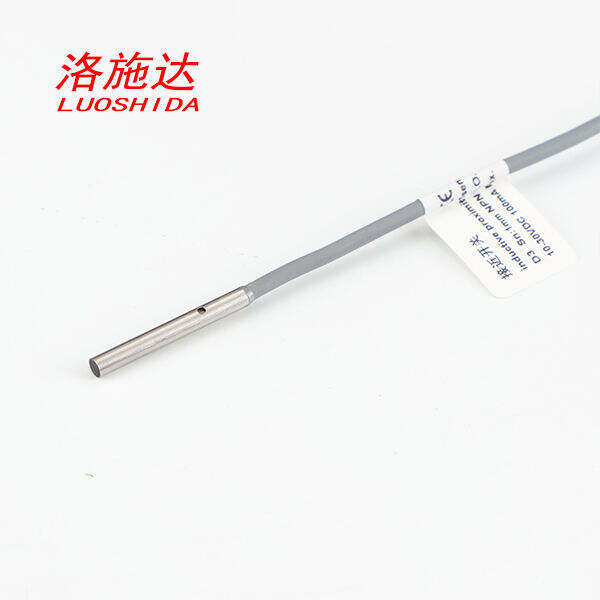
Implementing Sensor Technology in Your Protection Strategy
Installation Best Practices for Laser-Level Accuracy
Using laser-level sensors during installation is crucial for ensuring proper alignment, which significantly impacts sensor performance. These sensors provide precise measurements, reducing false readings and enhancing the reliability of moisture detection systems. To maintain accuracy over time, regular calibration according to manufacturer guidelines is essential. Routine calibration helps in compensating for potential sensor drift, ensuring they operate at their highest efficiency and reliability.
Maintenance Tips for Long-Term Sensor Reliability
Routine maintenance checks and cleanings are pivotal in extending the lifespan of moisture sensors. These activities involve using cleaning agents that do not damage sensor components, thereby maintaining their functionality and reliability. It is equally important to heed sensor alerts and promptly address any detected issues. Early problem-solving can prevent more complex issues down the line, securing the sensor's performance well into the future.