Improve Industrial Operations with Advanced Torque Sensors
The Critical Role of Torque Sensors in Industrial Efficiency
Enhancing Precision in Mechanical Systems
Torque sensors are vital in improving the precision of mechanical systems. They measure torque with high accuracy, thereby optimizing the performance and longevity of machinery. Accurate torque sensing helps to reduce wear and tear, ultimately enhancing the efficiency of operations. By investing in precise torque sensors, businesses can mitigate errors in assembly processes, significantly lowering the costs associated with warranty claims and repairs. Studies in the modern manufacturing landscape have shown that the integration of torque sensors could improve operational efficiency by up to 25%. This demonstrates the transformative impact that accurate torque measurement can have on industrial productivity, making it a crucial investment for companies aiming to optimize their manufacturing processes.
Applications in Automotive and Aerospace Manufacturing
In the automotive sector, torque sensors are indispensable for ensuring the correct tightness of components on assembly lines, which directly contributes to vehicle safety and reliability. These sensors help manufacturers avoid issues caused by improper assembly, ensuring that every vehicle meets stringent safety standards. Similarly, in the aerospace industry, torque sensors play a critical role in monitoring and controlling the torque applied during the assembly of critical components. This facilitates compliance with rigorous regulatory standards in aerospace manufacturing. Expert analysis suggests that by utilizing torque sensors, the occurrence of failures in high-stress components can be reduced by up to 30% in both automotive and aerospace applications. This reduction enhances the safety and durability of products, which is crucial for industries where precision and reliability are non-negotiable.
Synergy Between Torque Sensors and Proximity Detection Systems
Integrating Inductive Proximity Sensors for Safety
To bolster industrial safety, integrating inductive proximity sensors with torque sensors proves crucial. These sensors detect the position and presence of mechanical parts, ensuring machines operate safely by automatically disengaging systems during unsafe movements. This automation prevents potential accidents and minimizes equipment damage. The synergy between torque sensors and inductive proximity sensors greatly enhances safety protocols. According to studies, this integration can reduce workplace accidents by over 40%, highlighting its impact on industrial environments. Incorporating such advanced sensors is a proactive step in safeguarding workers and assets.
Photoelectric Sensor Types for Adaptive Automation
Photoelectric sensors, including reflective and through-beam types, significantly amplify the functionality of torque sensors in automated systems. By offering real-time data collection, these sensors help enhance the accuracy of torque measurements, especially in dynamic work environments. Implementing various photoelectric sensor types allows for streamlined operations that can adapt to different conditions while maintaining precision. This synergy not only improves torque measurement accuracy but also facilitates adaptive automation, crucial for the seamless operation of modern manufacturing processes. The ability to adjust and respond to real-time data ensures a high level of precision that is indispensable in maintaining efficiency and reducing errors.
Advanced Sensor Solutions for Precision-Driven Industries
M6mini Photoelectric Sensor: Compact Infrared Detection
The M6mini sensor stands out for its compact design and efficient infrared detection capabilities, making it ideal for space-constrained applications. Its ability to detect minute changes with high accuracy significantly enhances the capabilities of torque sensors in tight environments, where traditional sensors might struggle. In various industrial setups, users have reported substantial improvements in precision, highlighting the M6mini's effectiveness in enhancing sensor systems.
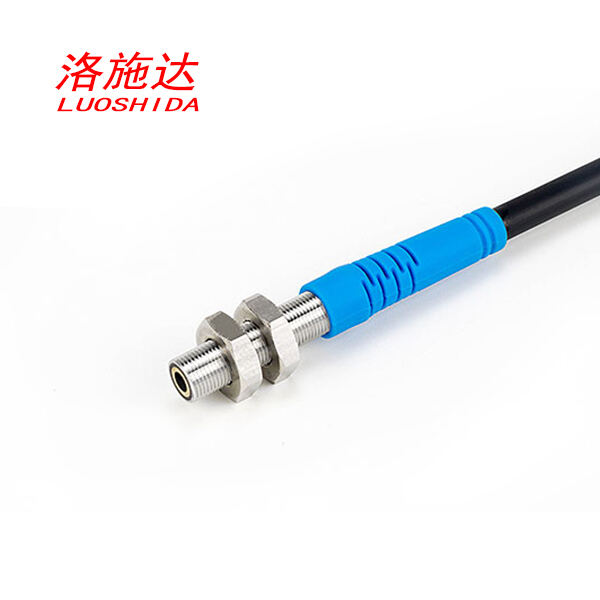
M8mini Photoelectric Sensor: Brass Nickel-Plated Durability
The M8mini sensor, with its robust brass nickel-plated construction, is designed to withstand harsh conditions, ensuring reliability crucial for maintaining torque sensor performance. Its rugged design not only supports high precision in critical applications but also significantly reduces maintenance requirements. Experts frequently recommend the M8mini sensor for industries demanding durability and consistent sensor performance, aiding in the longevity and stability of industrial operations.
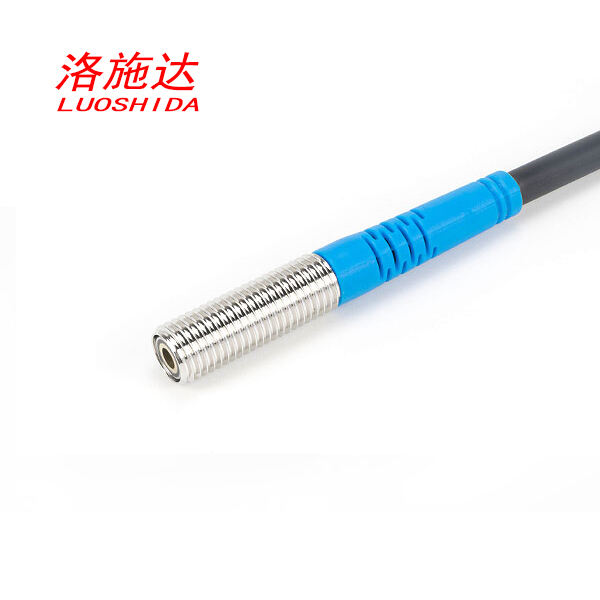
M18 Plastic Capacitive Sensor: IP67 Protection for Harsh Environments
The M18 plastic capacitive sensor, equipped with an IP67 protection rating, offers superior defense against dust and water, thus prolonging the life of torque measurement systems. Its functionality in extreme conditions makes it a preferred choice for outdoor applications in industries such as agriculture and construction. Statistical data indicates that equipment using IP67-rated sensors enjoys approximately 50% longer operational lifespan in challenging environments, validating the M18 sensor's robust design and reliability.
Key Benefits of Upgrading to Modern Torque Measurement Systems
Real-Time Data for Predictive Maintenance
Upgrading to modern torque measurement systems enables businesses to harness real-time data, facilitating predictive maintenance and minimizing unexpected downtimes and repair costs. Through the application of advanced analytics, these systems offer insights by examining torque fluctuation patterns to predict potential failures. This predictive approach helps in optimizing maintenance schedules, ensuring operational efficiency. Research indicates that companies utilizing predictive maintenance models have reported a substantial reduction in operational costs, ranging from 20% to 25%. This underscores the importance of integrating smart technology into torque measurement systems to promote reliability and cost-effectiveness.
Reducing Downtime with Wireless Connectivity
Modern torque measurement systems equipped with wireless connectivity provide significant advantages in reducing downtime. Wireless torque sensors facilitate seamless data transmission, enabling immediate responses to any discrepancies in torque measurements, thereby mitigating potential downtimes. This technology offers enhanced flexibility in system monitoring, allowing for timely adjustments and maintenance without the extensive downtimes typically associated with wired systems. Evidence from case studies demonstrates that wireless connectivity can reduce downtime by up to 30% compared to traditional wired setups, highlighting its effectiveness in maintaining smooth operations and enhancing productivity.